Video
Working Principle
Bio Balls function as carriers for biofilm growth, enabling effective biological filtration. The outer shell—molded from durable polypropylene—features a porous fishnet-like spherical structure, while the inner core consists of high-porosity polyurethane foam, offering strong microbial attachment and suspended solids interception. These features promote aerobic bacterial activity, supporting the breakdown of organic pollutants in aerobic and facultative bioreactors.
When introduced into a treatment system, the media float freely, continuously rotate with water flow, and maximize contact between water and microorganisms, leading to enhanced biological activity without clogging or the need for fixing.
Key Features
• High Specific Surface Area: Up to 1500 m²/m³ for efficient biofilm growth.
• Durable & Stable: Chemically resistant to acids and alkalis; withstands continuous temperatures of 80–90°C.
• Non-Clogging & Free-Floating: No need for brackets or support frames.
• High Porosity (≥97%): Promotes rapid microbial colonization and effective filtration.
• Safe & Eco-Friendly: Made from non-toxic materials; no harmful leachates.
• Long Service Life: Easy to maintain and replace, resistant to aging and deformation.
• Minimal Residual Sludge: Reduces maintenance costs over time.
• Esy Installation: Directly added to filtration tanks or systems.
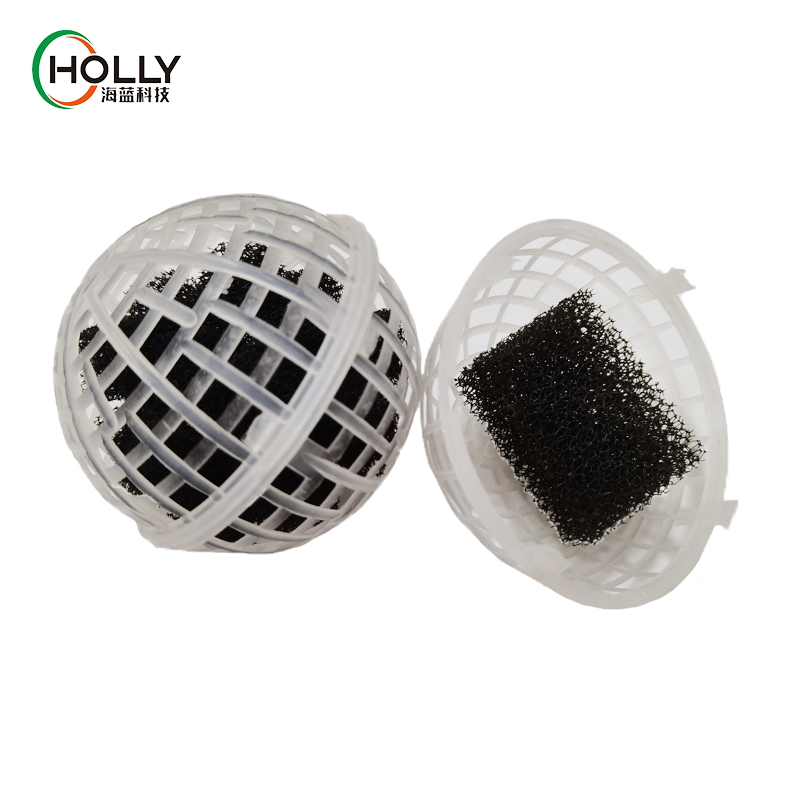
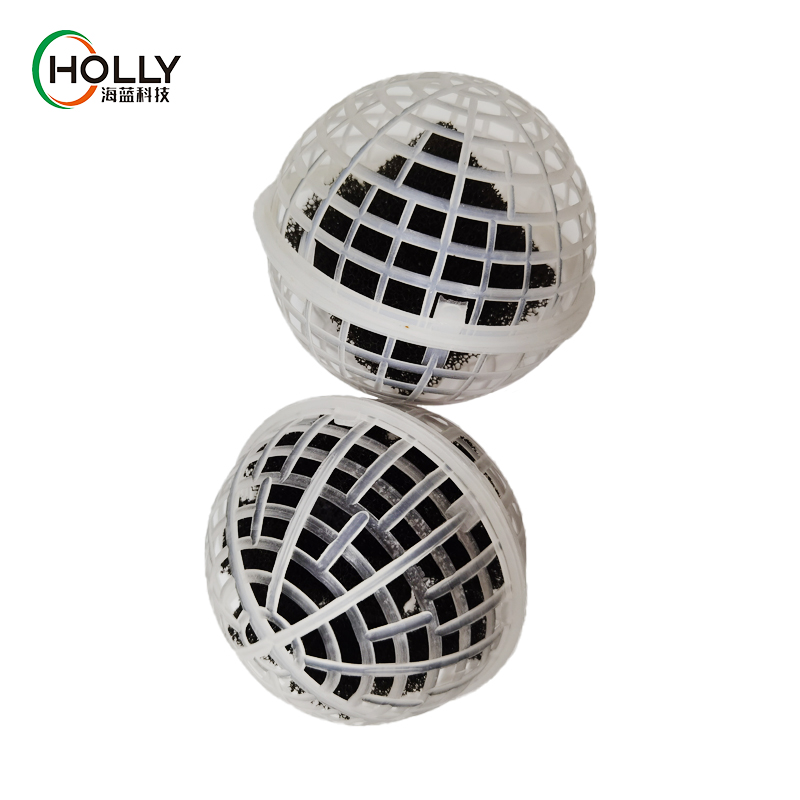
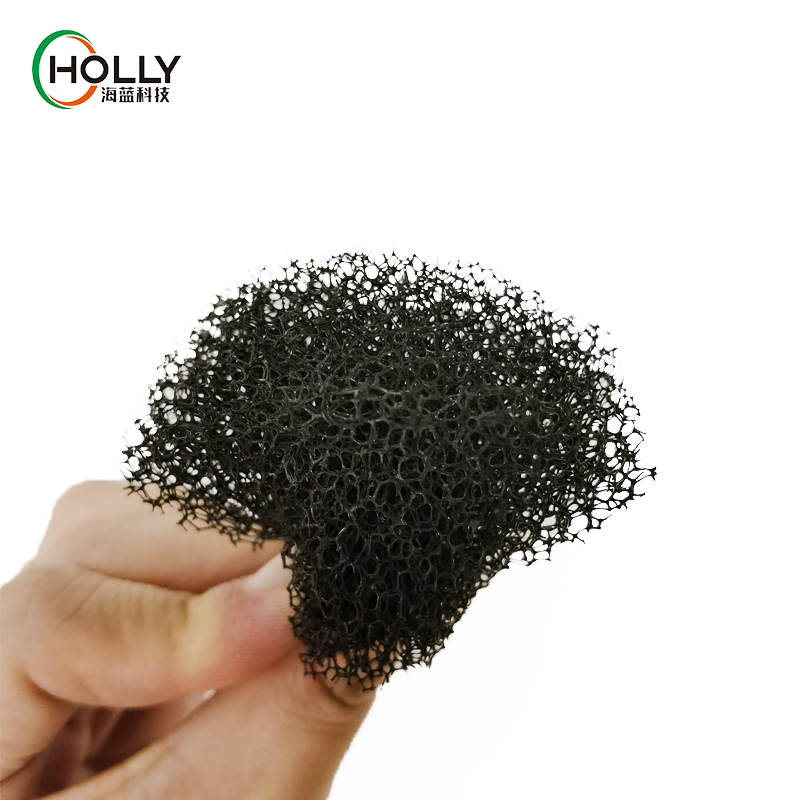
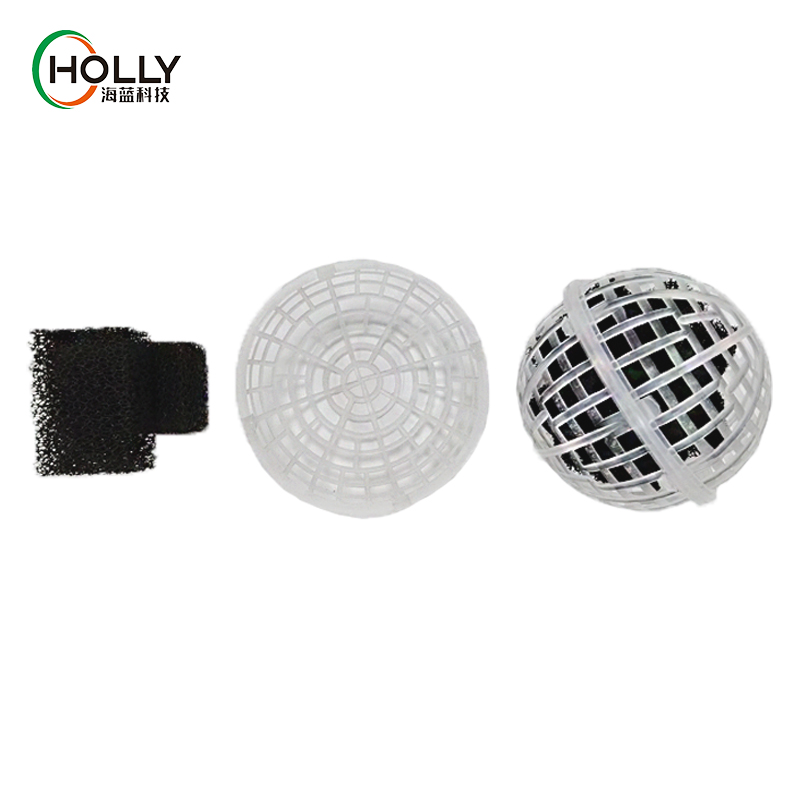
Applications
• Aquarium and Fish Tank Filtration (Freshwater or Pond).
• Koi Pond and Garden Water Features.
• Municipal Wastewater Treatment Plants.
• Industrial Wastewater Bioreactors.
• Biological Aerated Filters (BAF).
• MBR / MBBR / Integrated Biofilm Systems.
Technical Specifications
Diameter (mm) | Inner Filler | Quantity (pcs/m³) | Specific Surface Area (m²/m³) | Acid & Alkali Resistance | Heat Resistance (°C) | Embrittlement Temp (°C) | Porosity (%) |
100 | Polyurethane | 1000 | 700 | Stable | 80–90 | -10 | ≥97 |
80 | Polyurethane | 2000 | 1000–1500 | Stable | 80–90 | -10 | ≥97 |
Production & Quality
Production & Quality
Manufacturing Equipment: NPC140 plastic injection molding machine
Production Process:
1. Polypropylene injection molding to form the outer sphere.
2. Manual filling of polyurethane inner core.
3. Final assembly and quality inspection.
4. Packaging and shipping.